Combined with approach and diversion support, automated ground taxiing can reduce airport congestion. The combination also reduces workload on the flight deck and paves the way for intelligent automation in the air. A new Airbus UpNext demonstrator will show how this is done. It’s unconventional to say the least.
Commercial aviation is on a growth path. Experts predict that the global jetliner fleet will need to double in the next twenty years to meet demand.
One downside to this predicted traffic boom is that airports and airspace will become increasingly congested and more difficult for flight crews to navigate. Add to that an expected pilot shortage and you have the conditions for flight crew overload.
To avoid overload, three issues need to be addressed: relieving the burden on pilots, increasing safety through automated flight path monitoring and digitally supporting collaboration between flight crews and air traffic control.
Gate to gate support
For pilots, taxiing from the runway to the gate can be complicated. This makes it an ideal testing ground to address each of these three topics through intelligent automation.
So Airbus is doing what it has always done: innovating and demonstrating how this part of flying can be made even safer. The innovation arm of Airbus Next has launched Optimate: a next-generation autonomy demonstrator that demonstrates new capabilities while integrating features tested by its predecessors, such as: VERTEX And ATTOL.
The three-year project, a partnership with industry players, researchers and regulators including the French Civil Aviation Authority, aims to support pilots while increasing operational safety.
The ultimate goal of Optimate is to conduct a highly efficient automated gate-to-gate mission on an Airbus airliner. Each such mission will feature 4D trajectory management, a tablet-controlled networked virtual assistant and overridable protective measures – all to support the flight crew. Initially, however, the focus is on the rolling phase.
A “cockpit on wheels” packed with sensors
The Optimate soil test stand is… unusual. Sharp-eyed observers may have already spotted the distinctive lines and paint schemes beneath Airbus’ flight test aircraft at its base in Toulouse, France. The thing is: the test bench is actually a truck with the license plate OPTI1.
This cockpit on wheels is equipped with a virtual A350 flight deck that features “computer vision” devices including geolocation sensors, 4D radar and lidar, which together act as a virtual assistant to safely and automatically control an aircraft as it taxis. The back of the truck is equipped with a complete flight test installation to help engineers monitor testing.
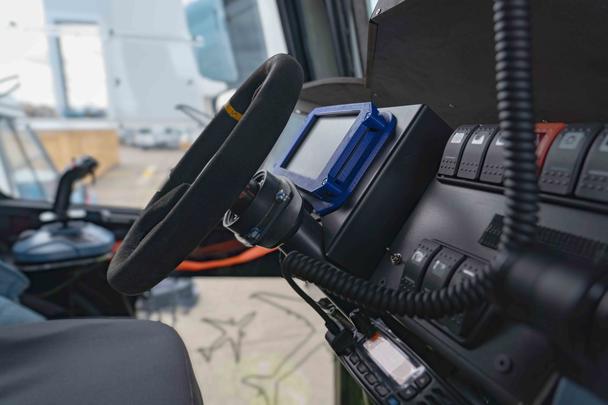
The all-electric “Flying Truck,” as the test stand is called, represents the type of functions that could one day relieve pilots’ workload. With fewer tasks to complete, flight crews can focus primarily on decision-making.
Thousands of hours of testing
The truck was first tested at UpNext’s headquarters near Toulouse and later on the runways of Blagnac Airport. Now the UpNext team hopes to expand the truck even further and take it to an international airport.
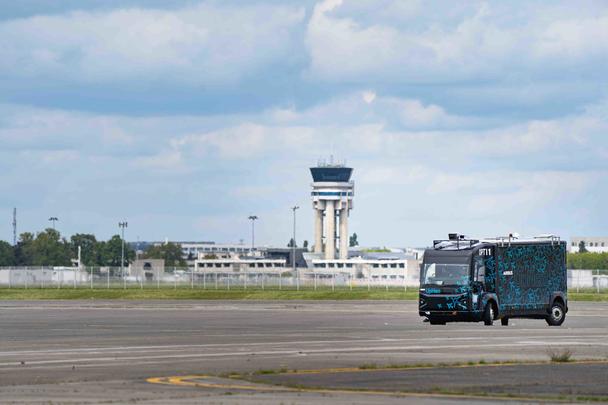
In the fourth quarter of 2024, Optimate will move up a gear with the demonstration of automated taxiing on board an Airbus A350-1000 test aircraft. During this phase, a prototype version of new automation features will be presented.
In the meantime, the “flying truck” will complete thousands of hours of testing. For Airbus, this keeps costs down, frees test pilots to focus on aircraft deliveries and ongoing certification campaigns, and reduces the project’s carbon footprint.2 Emissions. So, calling all aviation enthusiasts: F-OPTI has more to offer than meets the eye!